Summary:...
The gearbox is an industrial component, which can complete the power transmission task through the transmission gear train. At the same time, as a mechanical accessory for the transmission gear, the gearbox has a wide range of uses in the chemical industry. This article discusses the common fault performance and diagnosis measures of the gearbox in detail from the application of the gearbox.
1. The purpose of the gearbox
The main purpose of the gearbox is as follows: First, it can change the transmission speed through a gear set, and it is often called a "variable gearbox" in the industry. Secondly, the gearbox can change the rotational torque, that is to say, under the premise of the same power, the higher the speed of the gear, the smaller the torque on the gear shaft, and vice versa; again, the gearbox is used for power. Distribution, in industry, workers can use one engine to pull several slave shafts through the main shaft of the gearbox, and then only one engine will pull several loads; fourth, the gearbox has a clutch function, and the brake clutch is used With the gearbox clutch function, people can freely separate the two meshing gears, and then separate the load and the engine; fifth, to change the transmission direction, you might as well use two fan-shaped gears to make the force in it perpendicular The direction is transmitted to the axis of rotation on the other side in an orderly manner.
2. the performance of the typical failure of the gearbox
Through the analysis of the actual application of the gearbox, it is not difficult to determine its failure. The entire gearbox system includes components such as bearings, gears, transmission shafts and box structure. As a common mechanical power system, it is very prone to failures of mechanical parts, especially bearings, gears and transmissions, while it continues to move. For the three parts of the shaft, the probability of other failures is significantly lower than that of them.
When the gear performs its task, it lacks the ability to work due to various complex factors, and the value of the function parameter exceeds the maximum allowable critical value, which results in a typical gearbox failure. Its manifestations are also diverse. Looking at the overall situation, they are mainly divided into two categories: First, the gears are gradually produced during the accumulation of rotation, because the outer surface of the gearbox bears a relatively large load, and the gears mesh with each other. Relative rolling force and sliding force will appear in the gap. The friction force during sliding is exactly opposite to the direction of the two ends of the pole. Over time, long-term mechanical operation will cause the gears to glue, cracks, and increase the degree of wear. Gear fractures will become Inevitable. Another type of failure is caused by the staff being unfamiliar with the safe operation process or violating the operating specifications and requirements, negligence in installing the gear, or the hidden danger of the failure in the initial manufacturing. This failure is often caused by The inner hole and the outer circle of the gear are not on the same circle center, and the shape of the gear meshing with each other has errors and asymmetrical axis distribution.
In addition, in each part of the gearbox, the shaft is also a part that is easy to lose. When a relatively large load impacts the shaft, the shaft will quickly deform, which directly induces this failure of the gearbox. . When diagnosing gearbox faults, the effects of shafts with different degrees of deformation on gearbox faults are inconsistent. Of course, there will be different fault performances during this period. Therefore, the shaft distortion can also be divided into severe and mild. . The imbalance of the shaft will cause failures. The reasons are as follows: working in a heavy load environment, it is inevitable to deform over time; the shaft itself exposes a series of defects in many processes such as production, manufacturing and processing, resulting in newly cast The axis will show a serious imbalance.
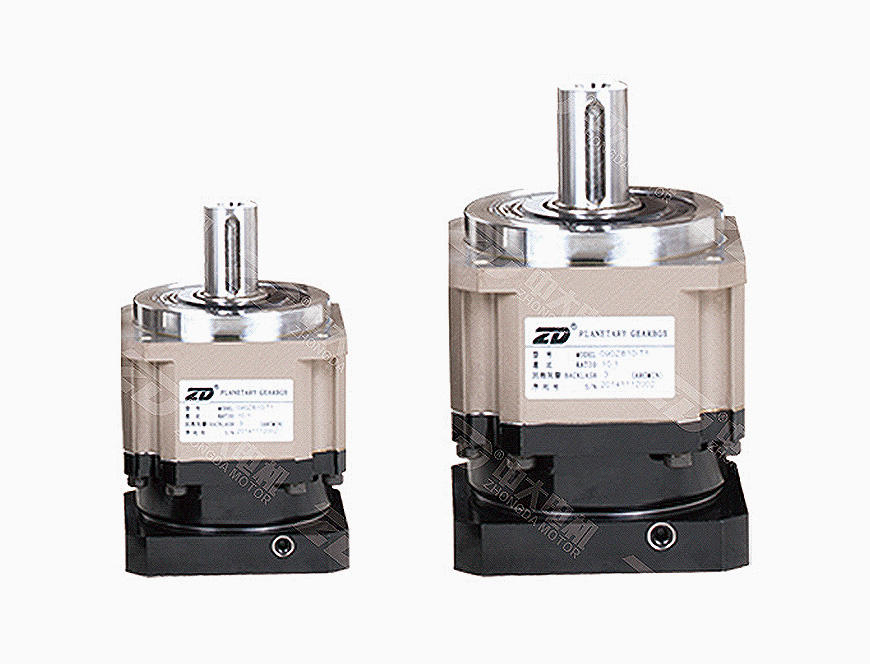
3. the strategy of
planetary gearbox fault diagnosis
Gearbox is a unified mechanical body in which gears and bearings coexist. All kinds of failures caused by machining defects or pressure are worthy of attention. Generally speaking, the following methods are usually used:
a. Cepstrum analysis method
Cepstrum analysis, also called secondary spectrum analysis, is a new technology in modern signal processing science. When the spectrogram of the mechanical signal has multi-group modulation side frequencies that are difficult to identify, the cepstrum can decompose and identify the fault frequency, analyze and diagnose the cause of the fault.
For the gearbox vibration spectrogram with several pairs of gears meshing with each other, because each pair of gears will have sidebands when meshing, when the individual sidebands are intertwined and concentrated, it is far more difficult to identify and analyze the frequency. Not enough, because the cepstrum will convert the harmonics in the power spectrum into a single spectrum line in the cepstrum graph, and its position implies that the corresponding harmonic frequencies in the power spectrum are separated by a period of time.
Another significant advantage of cepstrum is that it is not sensitive to the signal transmission path of the sensor or the orientation of the measuring point, and it is not sensitive to the correlation between the frequency control and the amplitude value, which in turn helps to monitor the magnitude of the fault signal. Measure the specific value of the amplitude of a certain measuring point.
b. Sideband analysis method
Generally speaking, the sidebands are analyzed from two aspects. One is to compare the variation range of the sideband amplitude during each measurement; the other is to check the specific frequency relationship with the help of the symmetrical characteristics of the sideband frequency to determine whether it is the same. If it is the sideband of the group, the frequency value of the modulation signal and the meshing frequency of the gear box can be obtained along the way.
It should be pointed out that individual faults such as gear shedding, cracks on the tooth root and individual broken teeth will have obvious transient modulations. There will also be a series of sidebands at the meshing position and on both sides. Their characteristics are mainly The order is relatively dense and the spectral lines are scattered. The shape of the side frequency is different due to the stacking of high-order frequency conversions. If there is an obvious local fault, it can also promote the harmonic components and the frequency of rotation to rise.
The sideband component here contains sufficient gearbox fault information resources. To obtain this information, sufficient frequency resolution is required during spectrum analysis, so as to facilitate accurate measurement of the distance between the sidebands.